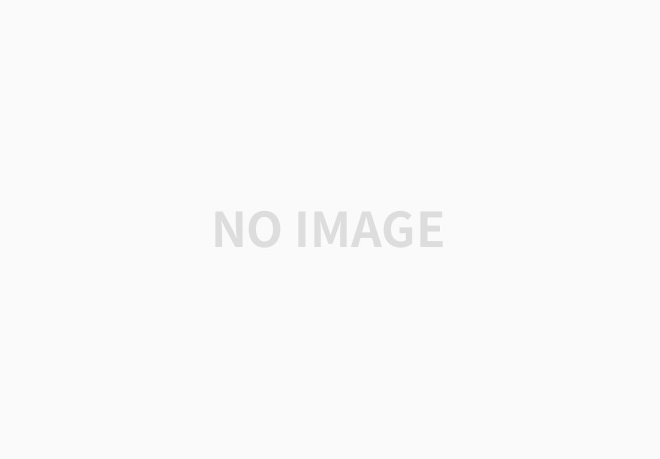
안녕하세요 !
SPM Instrument KOREA 입니다 😁
이전 포스팅에서도 몇 번 언급한 바와 같이, 베어링의 컨디션 모니터링은 회전 설비의 효율적이고 안정적인 운영을 위해 필수적입니다.
하나의 기계 시스템 안에서 핵심적인 역할을 수행하는 베어링은 그 상태를 실시간으로 감시하고 관리함으로 설비의 성능, 안정성, 비용 효율성에 직접적인 영향을 끼칠 수 있습니다.
오늘은 전의 포스팅에 이어서 베어링의 컨디션 모니터링에 대한 이야기를 나누어 보도록 하겠습니다 !
베어링 고장 원인
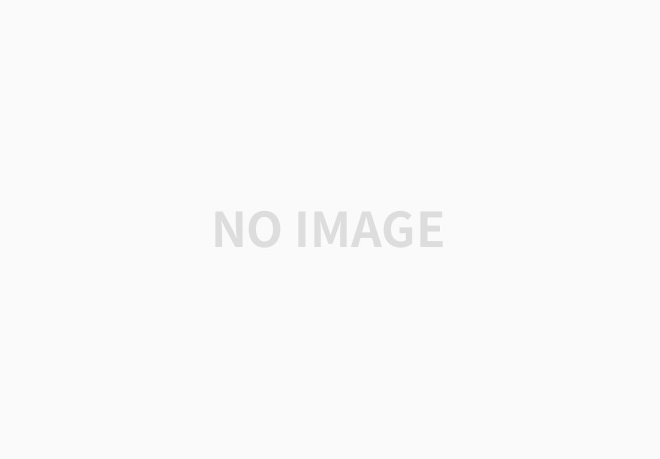
베어링은 회전 설비의 핵심 부품으로, 베어링 상태 모니터링을 통하여 상태를 지속적으로 감시하여 고장이나 이상을 조기에 감지할 수 있습니다 !
이러한 베어링 상태 모니터링은 설비의 안전성과 효율성을 유지하며, 예상하지 못한 다운타임을 방지합니다.
베어링의 고장은 기계의 성능 저하 및 심각한 고장을 유발할 수 있습니다.
여기서 베어링은 회전 설비에서 축과 하우징 사이의 하중을 지지하는 핵심 부품으로써의 역할을 하며, 여기서 고장은 회전 설비의 계획되지 않은 정지와 이로 인한 비용을 초래합니다.
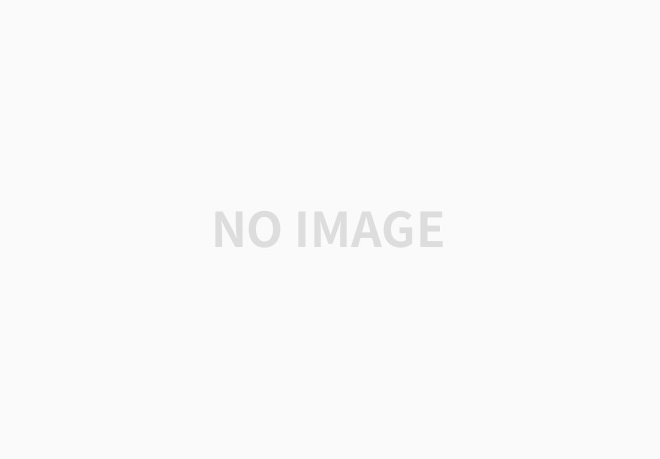
그렇다면 베어링의 일반적인 고장 원인을 다시 정리해 보도록 하겠습니다 :)
1. 윤활 문제
부적절한 윤활 : 과도하거나 부족한 윤활 상태는 베어링의 마찰 및 온도 상승 등으로 고장이 발생
윤활유 오염 : 윤활유에 먼지 등의 이물질이 혼입 되어 베어링의 표면 손상 유발
윤활유 열화 : 윤활유 품질 저하로 인하여 윤활 성능 감소
2. 과도한 하중
설계 하중 이상으로 인한 압박으로 표면에 균열 및 피로 손상 발생
축 방향 하중 혹은 방사 방향 하중이 설계 기준 초과하면 베어링 파손 가능성 증가
3. 진동 및 충격
외부 진동 및 충격으로 인하여 베어링 내부 마모, 균열 그리고 변형 발생
회전 설비의 불균형, 정렬 불량 등이 주요 원인이 됨
4. 설치 및 정렬 불량
베어링 설치 시 정렬 잘못되어 균등하지 못한 하중 분포로 인한 특정 부분의 과도한 마모 발생
축과 베어링 하우징 불균형이 회전 시 진동과 열 발생
5. 온도 문제
고온에서 작동하면 윤활유가 열화 되어 베어링 금속 표면 연화
저온에서 자동하면 윤활유가 경화되어 윤활 성능 저하
6. 부적절한 유지 보수
정기적 점검 부족으로 인한 초기 결함 발견 미흡
부적절한 부품 교체 작업으로 오염, 잘못된 조립, 부품 손상의 문제 야기
이 외에도 다양한 고장 원인이 존재합니다.
베어링 고장 원인을 미리 파악하고 방지하기 위해 컨디션 모니터링, 정기 점검 등 적절한 조치를 취하여 주는 것이 중요합니다 !
이를 통하여 시스템 안정성을 유지하고, 고장 발생으로 인한 비용과 시간을 절약할 수 있습니다 ( •̀ .̫ •́ )✧
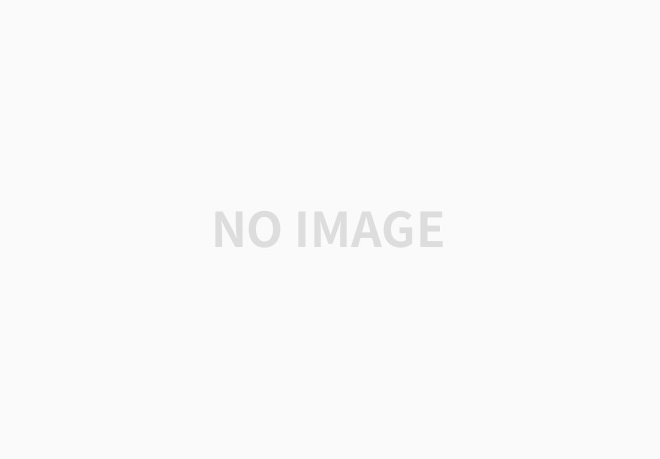
베어링 고장이 발생했다는 주요한 징후가 있습니다 !
- 이상진동 발생 : 고장이 진행될수록 진동이 심해집니다.
- 이상 소음 : 베어링 결합부 사이 삐걱거리거나 충격음이 발생합니다.
- 과도한 온도 상승 : 고장 초기 단계에 온도 상승이 관찰될 수 있습니다.
- 윤활 상태의 저하 : 윤활유가 변질되거나 누출될 경우에 윤활의 성능이 저하됩니다
진단 신호 지표
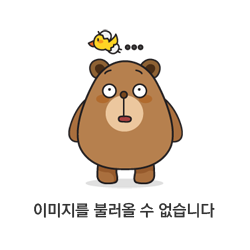
위와 같이 베어링 결함을 탐지할 때 사용되는 지표에 대해 이야기해 드리겠습니다 !
- 베어링 고유 주파수 : 외륜, 내륜, 볼의 결함 위치별로 고유 주파수를 계산
- BPFI (Ball Pass Frequency of Inner race)
- BPFO (Ball Pass Frequency of Outer race)
- FTF (Fundamental Train Frequency)
- BSF (Ball Spin Frequency)
- FFT (Fast Fourier Transform) : 진동 신호 주파수 스펙트럼 분석에 사용
- Envelope Analysis : 미세한 결함 신호를 증폭하여 이상 탐지
베어링 상태 모니터링 이점
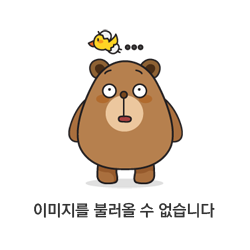
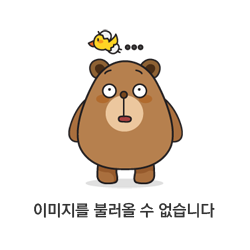
베어링 결함에 대한 컨디션 모니터링을 통하여 회전 설비에서 중요한 부품인 베어링의 상태를 지속적으로 감시할 수 있게 됩니다.
이를 통하여 설비 운영 효율성과 비용 절감 등의 다양한 이점이 따르게 되는데, 그에 대해 정리해서 이야기해 드리도록 하겠습니다 !
1. 조기 결함 탐지
베어링 결함이 초기 단계에서 발견되어 주요 부품이나 설비 전체에 영향을 미치기 전에 조치할 수 있습니다 !
이를 통하여 고장으로 인한 다운타임을 줄여 설비 운영 안정성을 확보합니다.
2. 유지 보수 비용 절감
정해진 주기가 아니라, 실제 설비의 상태를 기반으로 유지 보수 계획을 세우기 때문에 불필요한 정비 작업이 감소됩니다 !
이에 따라 초기 결함 단계에서 수리하면 복구 비용이 저렴하며 관련 부품 손상 방지로 인한 추가 비용을 절약할 수 있습니다.
3. 설비 가동 시간 증가
계획되지 않은 설비 가동 중지 시간을 줄여 생산성을 유지함으로 가동률이 향상됩니다 !
그렇기 때문에 예상치 못한 다운타임 없이 계획된 운영이 가능하여 생산 일정이 최적화됩니다.
4. 베어링 및 기계 수명 연장
베어링에 결함이 확산되기 전에 문제를 해결하여 부품의 수명을 연장시킬 수 있습니다 !
이렇게 베어링 상태가 최적화되어 기계 성능도 안정적으로 유지할 수 있게 됩니다.
5. 에너지 효율 개선
베어링의 상태가 양호하면 마찰이 감소하여 불필요한 에너지의 손실을 줄일 수 있습니다 !
적절한 베어링의 윤활 관리로 인하여 진동 감소로 전반적인 에너지 효율을 향상시킵니다.
6. 안전성 향상
베어링 고장으로 인한 기계적 사고를 미연에 방지할 수 있습니다 !
또한 진동, 소음, 열 발생 등 문제가 감소하여 작업 환경 또한 개선되어 작업자가 산업 현장에서 원활하게 작업할 수 있습니다.
7. 데이터 기반 의사결정 지원
모니터링을 통한 데이터를 통한 유지보수의 시점, 설비 상태 분석으로 최적의 운영 방안을 결정할 수 있습니다 !
이렇게 축적된 데이터를 기반으로 고장의 원인을 분석하고 개선할 수 있습니다.
8. 최신 기술과 연계한 시너지 효과 기대
IoT 및 AI를 활용한 실시간 모니터링 및 예측 모델을 통하여 최적의 솔루션을 제공할 수 있게 됩니다 !
또한 디지털 트윈을 이용하여 설비의 가상 모델과 연계해 더욱 정밀한 상태 진단이 가능합니다.
베어링 모니터링 SPM 측정 기술

1. SPM HD
SPM HD 측정 기술은 특허 출원된 SPM고유의 방법입니다 !
첨단 디지털 기술 및 RPM 기반 샘플링 주파수를 적용하여 특히 저속 회전 설비 베어링의 상태 측정, 평가에서 유용한 유일한 기술이라고 할 수 있습니다 😆
구름 요소 베어링의 상태를 간편하고 신속하게 진단하는 기술로, 그 신뢰성을 높이 평가받는 SPM(Shock Pulse Method)의 최신 기술입니다 :)
베어링은 사용 기간 중 부하가 가해진 구름 요소와 레이스 사이에서 Shock Pulse를 발생시킵니다.
이 쇼크가 크기에 비례하여 전기적 펄스를 출력하는 SPM Transducer를 반응하게 하여, 32KHz 공진 주파수에 반응하여 진폭에 따라 계량화가 가능합니다.
2. SPM dBm/dBc
Shock Pulse Method는 회전 설비 베어링의 상태 판정을 위하여 구름베어링에서 발생하는 신호를 분석하는 SPM의 특허 방식입니다.
이러한 쇼크펄스 측정 장비는 2가지 진폭 레벨이 결정될 때까지 측정 임계값을 변화시키면서 초당 발생하는 쇼크펄스의 발생 빈도를 계산하여 진폭을 측정합니다.
여기서, dBc는 쇼크의 바닥값을 나타냅니다.
대략 초당 200번 발생하는 값으로 dBc(decibel carpet value)로 표시합니다 :D
dBm은 쇼크 피크값을 나타냅니다.
2초 동안 발생한 쇼크 펄스의 피크 값으로, dBm(decibel maximum value)로 표시합니다 :D
점멸 지시계 혹은 이어폰을 사용하여 더 이상 검출되는 신호가 없을 때까지 측정 임계값을 상승시키며 쇼크값을 설정합니다.
3. SPM LR/HR
SPM LR/HR 기술은 기존 구름 요소 베어링 진단을 위한 Shock Pulse Method에서 윤활 상태 진단 기능을 추가하여 발전시킨 기술입니다.
회전하는 계면에서 정밀한 유막 상태 분석이 가능하며 최상의 윤활제를 선정할 수 있습니다 !
SPM LR/HR 기술에 사용되는 SPM Transducer와 측정 방식은 SPM dBm/dBc와 동일합니다.
HR은 쇼크펄스의 하이 레이트로, 대략 초당 100회 발생하는 쇼크의 바닥값을 나타냅니다.
LR은 쇼크펄스의 로우 레이트로, 대략 초당 40회 발생하는 강한 쇼크의 값입니다.
베어링의 윤활 및 손상 여부는 측정된 쇼크펄스 바닥값, 피크값, 베어링 형태, 사이즈, 속도 등을 고려하여 판정됩니다 :D
베어링 상태 모니터링 시스템으로 인하여 조직의 유지 관리 전략이 효과적으로 수행할 수 있게 됩니다.
이미 고장이 발생하고 난 후의 교체 및 수리가 아닌, 그 이전에 확인하고 예방할 수 있게 됩니다 !
다시 말해서, 산업체의 설비가 고장으로 이어지기 이전에 문제를 파악하여 유지 보수 비용을 절감하고 생산성을 높일 수 있게 됩니다 🤗
베어링의 상태 모니터링을 통하여 정비 비용이 절감되며, 설비 수명이 연장되고, 제품 생산성 향상과 같은 효과를 기대할 수 있습니다 :D
베어링의 컨디션 모니터링은 단순한 유지 보수를 넘어 설비의 운영 최적화와 지속 가능성 확보라는 관점에서 중요한 역할을 수행합니다 👍
저희 SPM KOREA가 여러분 소중한 설비에 결함이 발생하여 다운타임으로 이어지지 않도록 상태를 모니터링하여 진단할 수 있는 솔루션을 제공해 드릴 수 있습니다 :D
다음에도 유익한 정보를 가지고 돌아오도록 하겠습니다.
감사합니다 ❤
참고 자료 :
SPM HD
SPM HD 측정 기술은 특허 출원된 SPM 고유의 방법으로 구름 요소 베어링의 상태를 간편하고 신속하게 진단하는 기술로 그 신뢰성을 높이 평가받는 SPM(Shock Pulse Method)의 최신 기술입니다. 첨단 디지
spminstrumentkorea.co.kr
2024.07.04 - [Industry News/산업 정보] - 산업용 베어링 고장의 일반적 원인과 문제 해결 방법 / Bearing / Common Bearing Problem
산업용 베어링 고장의 일반적 원인과 문제 해결 방법 / Bearing / Common Bearing Problem
안녕하세요 !SPM Instrument KOREA 입니다 😁 저희는 여러 번 산업 현장에서 중요하게 여겨지는 베어링에 대하여 이야기를 나누었습니다.오늘도 저는 베어링에 관한 키워드를 선택하지 않을 수 없었
spminstrumentkorea.tistory.com
'Industry News > 산업 정보' 카테고리의 다른 글
[예방 정비] 회전 설비 고장 진단 (0) | 2024.12.12 |
---|---|
[예방 정비] 상태 기반 예방 정비 / Condition-Based Maintenance / 의미와 중요성 (1) | 2024.12.06 |
[회전 장비] 베어링 / Bearing / Rolling Bearing / 베어링 유형 및 쓰임 (2) | 2024.11.22 |
[기계 설비] 섬유 산업 / 컨디션 모니터링 / Fiber Industry / Condition Monitoring System (3) | 2024.11.08 |
[기계 설비] 전자 및 반도체 산업 / Electronics / Condition Monitoring System (4) | 2024.11.01 |
댓글